Parts Manufacturer
Machining Parts for OEM customers
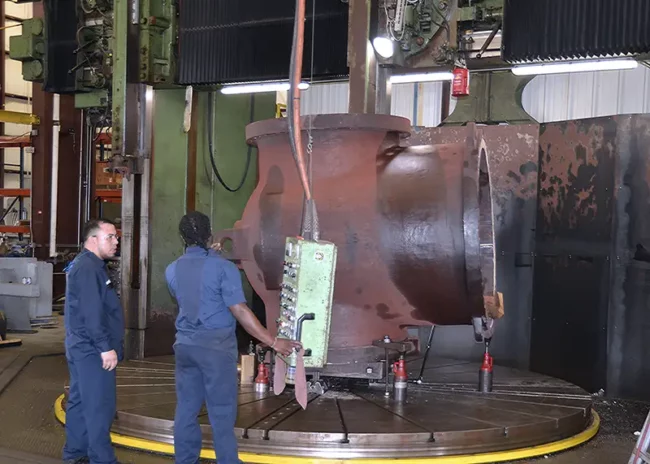
Extensive CNC Machining Capabilities
The CNC department contains seven machines:- 3 turning centers
- 2 small vertical mills
- Large horizontal machining center
- Large four axis turning center
Copyright © 2025 United Valve, All Rights Reserved. Sitemap. Houston SEO Web Design by Bizopia